In the world of e-commerce, returns are an inevitable part of the business. Whether it's…
Unlocking Success: The Importance of KPIs
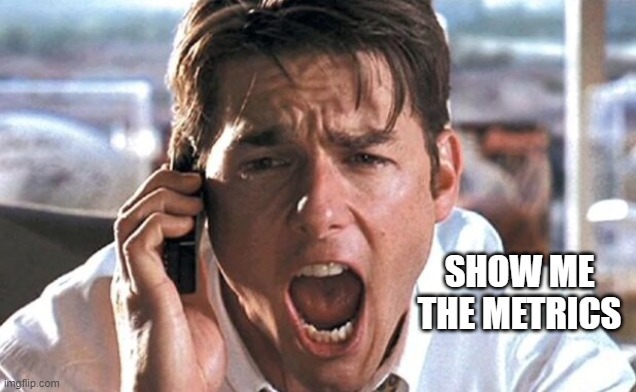
In the realm of logistics and supply chain management, warehouses serve as crucial hubs where efficiency, accuracy, and timeliness are paramount. The ability to effectively measure and improve performance within these facilities is essential for meeting customer demands, minimizing costs, and sustaining competitive advantage. This is where Key Performance Indicators (KPIs) play a pivotal role, providing valuable insights into operational health and guiding strategic decision-making. Let’s explore some of the key warehouse KPIs that every logistics manager should prioritize.
1. Inventory Accuracy
Inventory accuracy is foundational to warehouse operations. It measures the percentage of inventory items that are correctly recorded in the system compared to the physical count. High accuracy ensures that orders are fulfilled correctly and on time, reduces stockouts, and minimizes the risk of overstocking. This KPI helps identify discrepancies, assesses the effectiveness of inventory management practices, and informs strategies for improving data integrity and visibility.
2. Employee Productivity
Employee productivity measures the output per warehouse employee over a specific period, typically in terms of units picked, packed, or shipped. Optimizing employee productivity ensures efficient labor utilization, reduces labor costs, and enhances overall operational efficiency. This KPI helps warehouses evaluate workforce performance, identify training needs, and implement incentive programs to motivate employees and improve productivity levels.
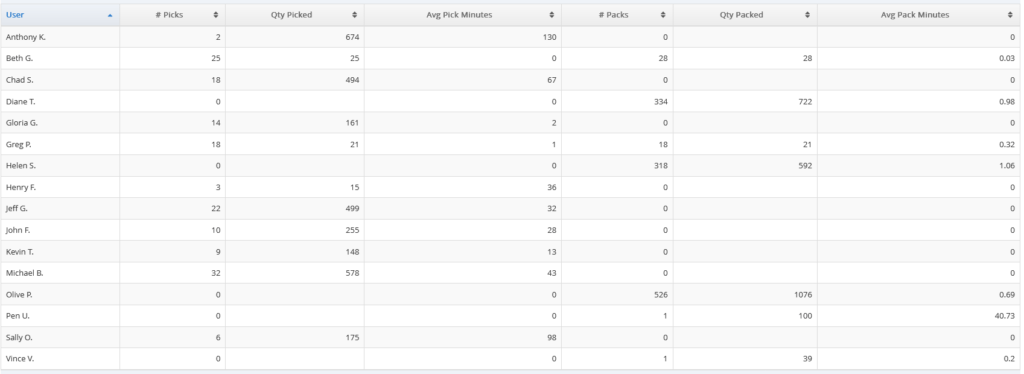
3. Warehouse Capacity Utilization
Warehouse capacity utilization assesses the percentage of available storage space that is currently in use. Efficient use of warehouse space maximizes storage capacity, minimizes storage costs, and improves operational efficiency. This KPI enables warehouses to plan for future growth, optimize layout and storage configurations, and implement strategies to minimize unused space or congestion.
4. On-Time Shipping
On-time shipping reflects the percentage of orders shipped by the promised date or within the specified timeframe. Timely shipments are critical for meeting customer expectations, reducing transportation costs, and improving overall supply chain efficiency. This KPI helps warehouses assess their ability to fulfill orders promptly, identify delays in processing or fulfillment, and implement measures to enhance shipping schedules.
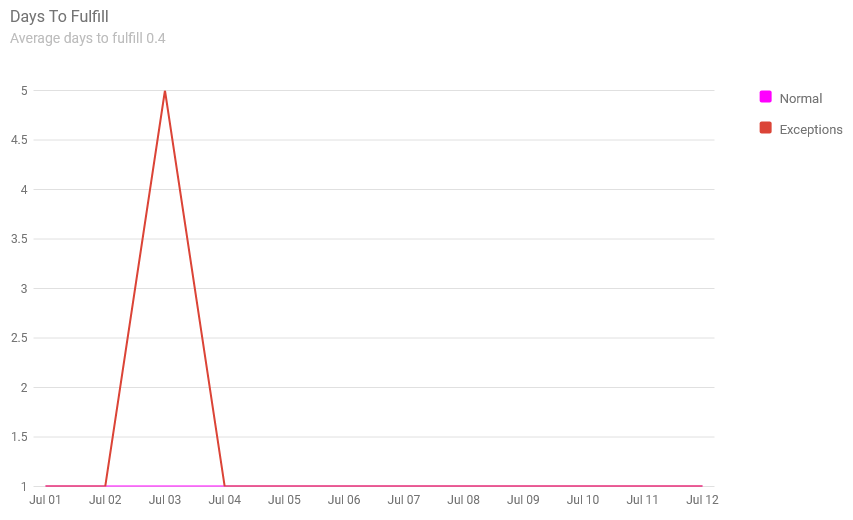
5. Order Picking Accuracy
Order picking accuracy measures the percentage of orders picked without errors compared to the total number of orders fulfilled. Accurate picking reduces fulfillment times, minimizes returns and rework, and enhances customer satisfaction. Monitoring this KPI allows warehouses to identify bottlenecks in picking processes, optimize picking routes, and implement training programs to improve accuracy rates.
Get in touch with us today to discover how Fulcrum’s KPI Suite can transform your warehouse!
This Post Has 0 Comments